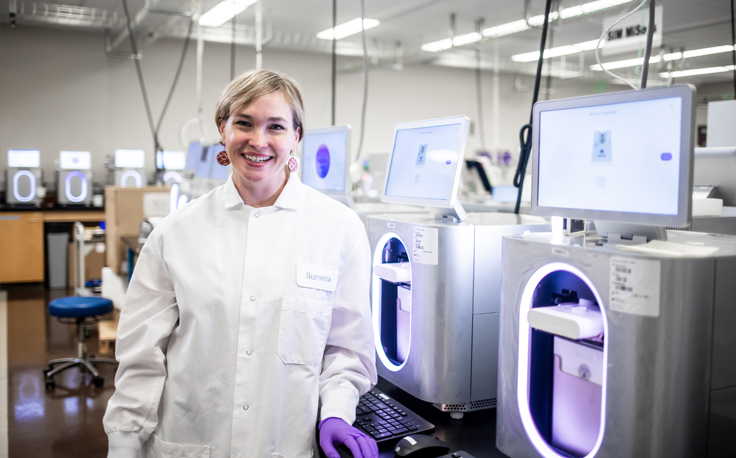
December 4, 2024
Illumina recently launched the MiSeq i100 and MiSeq i100 Plus Systems, two powerful, compact benchtop sequencers that incorporate more than 140 invention disclosures and 60 patent families. On our News Center, we are celebrating outstanding employees who helped develop this breakthrough technology.
"If you're a kid who likes science, you sort of assume that your pick of profession is either a veterinarian, doctor, or astronaut,” says Illumina Associate Director of Scientific Research Erin Imsand. “No one tells you you can make technology that makes a difference in the world.”
In her academic and professional careers, Imsand has immersed herself in several different scientific disciplines—and this cross-functional experience has served her well. In fact, it may be her secret sauce.
She earned her bachelor’s in chemical engineering and researched green energy in a project commissioned by Hyundai. She received a PhD in biochemistry—having never taken an undergraduate course in the subject. She ran a yeast biochemistry team making biofuels for BP before she realized that clean energy was moving toward electric vehicles. “It became pretty clear that I was not going to see the launch of anything I was working on,” she says, “and that really matters to me.”
At the time, Imsand had friends working at Illumina who said they “definitely launched products.” She remembers thinking that launching products would fill her soul a little more. Imsand joined Illumina seven years ago in what was then called Life Cycle Management.
With a background in engineering and basic sciences, she fit nicely in Operations, in between the development scientists and the manufacturing team. She started working on some of Illumina’s oncology products, such as TruSight Oncology 500.
After about a year and a half, Imsand was approached about a project still in the concept stage—what would become the NovaSeq X. She was asked to help incorporate lyophilization (better known as “freeze drying”) into the product’s sequencing reagents, which had previously required dry ice shipping and cold storage. If they could pull it off, the process could stabilize reagent biomolecules, raising the temperature at which they could be shipped. Through a lot of hard work, Imsand and a team of scientists were able to map out a way to design the first Illumina product to use lyophilization—and ambient shipping.
But lyophilization of sequencing reagents could be pushed further—in addition to shipping, what if the reagents could be stored at room temperature? Imsand, having now moved to R&D, got the chance to experiment when she was asked to run the entire reagent team for the new MiSeq i100 project.
“Liquid is like a mosh pit for biomolecules,” she says. “They can jump around and crash into each other, and that mobility can drive the shelf life and thermal stability really, really low. That’s why we tend to freeze our reagents.” However, she explains, freezing only minimizes molecular mobility—it doesn’t stop it completely. Ice crystals can actually move in the frozen solid. Lyophilization uses a partial vacuum chamber to reduce the atmospheric pressure on a frozen material to the point where its water ice can transition directly from solid to gas, a process called sublimation. This removes nearly all the water content from the materialthe same way food is freeze dried. What remains is a dry powder or cake (like with NovaSeq X) or, in the case of the MiSeq i100, microspheres. A cartridge is filled with these solid little dry balls, which are later rehydrated on the instrument.
Lyophilization enables these new reagents to last far longer than previous versions, and the cartridges don’t need to thaw before use. “I think customers are really, really going to love being able to store the reagents on the benchtop,” Imsand says. “No more refrigerator space required. No more freezer space required.”
In addition to the microspheres, her team also developed the enzymes, fully functionalized nucleotides, and other materials that go into the reagents. Depending on the current phase of whichever program they’re working on, their activities range quite widely, from developing analytical methods, raw materials, or formulations, to establishing the processes to make them. Over the course of three years, she has worked closely with a number of teams, including the flow cell team (her reagents work on the flow cell), the cartridge team (who fill the cartridges with microspheres) and the operations team, whom they collaborated with to transfer the microsphere-making technology into a robust manufacturing process that’s continuously reproducible.
An evolving field and industry
What does it take to work with someone like Erin Imsand? “With our movement into lyophilization, we have graduated into a brave new world where you have to be a little bit equipment engineer, a little bit process engineer, a lot chemist,” she says. An ideal candidate is “someone who’s fearless, because there’s not a ton of industry precedent for what we’re doing.” The ideal candidate can also integrate multiple requirements into one system. “A lyophilized reagent, for example, has to be moisture tolerant; it can’t be super staticky or super foamy. You have to be able to think outside the box and not get too discouraged by hard problems.” Imsand adds that a person could have a PhD or not, a background in manufacturing, basic chemistry, engineering, or another area, and still be very successful on her team. “What’s nice is there’s almost no way you could come in with all the experience needed. You have to learn on the job.”
On the heels of launching two products that use lyophilization, Imsand envisions an exciting and innovative future for the genomics industry, and one that welcomes all kinds of talent. “We were the first company to do clustering chemistry on the sequencer—you used to have to buy two different instruments, one to do clustering, one to do the actual sequencing,” she says. “We made a patterned flow cell using a more cost-efficient manufacturing process to help drive sequencing costs down. We’ve had these big step changes in the industry driven by Illumina. I think lyophilization is going to be one of these next really big steps and I can’t wait to recognize my team. They were part of this, they did it, they pioneered it, and now we’ve just set a precedent that others will be following for the next decade.” ◆